Laser impregnation
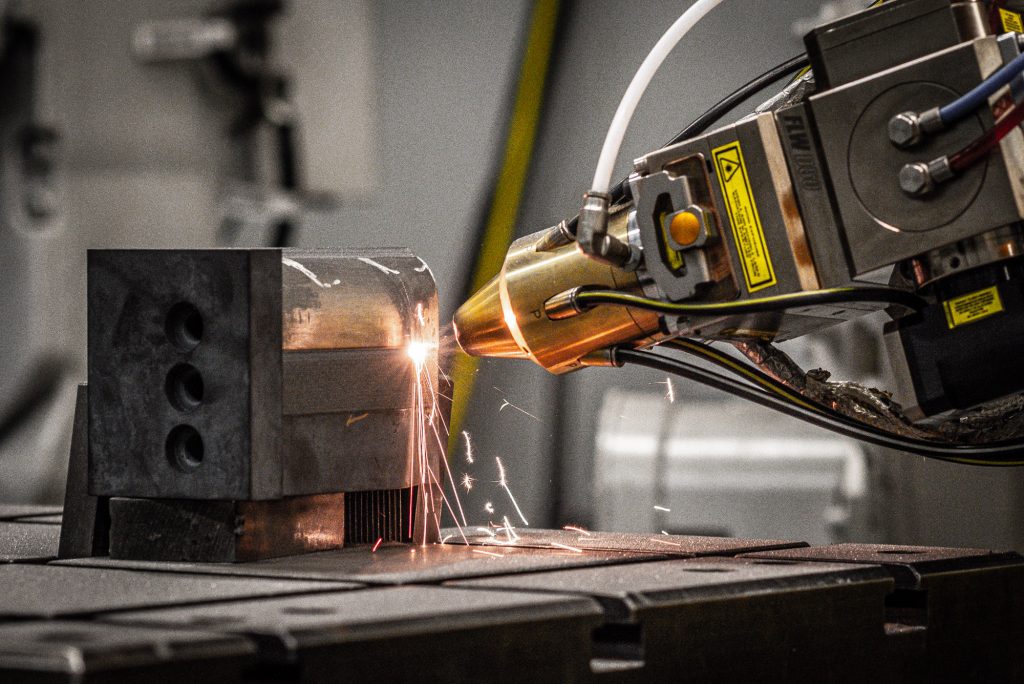
ABOUT THE METHOD
Laser impregnation is a very effective method for creating surfaces with extreme abrasion resistance. The surface of the base material is melted with a laser, and ceramics are injected into the molten surface. The method provides an extreme abrasion resistance of metallic materials that has no equivalent in traditional methods. It is a successful surface treatment method for components that are exposed to wear and high stress along with high temperatures or corrosive environments. This can be, for example, production equipment in rolling mills or wear-exposed tool surfaces. Laser impregnation provides an extreme, local hardness. Since you can impregnate local hardness on the surface, you can be more generous in the choice of base material. For example, you may want to use a cheaper raw material as a softer base material, which is better from a processing and vibration point of view. Nevertheless, the desired hardness is obtained where required.
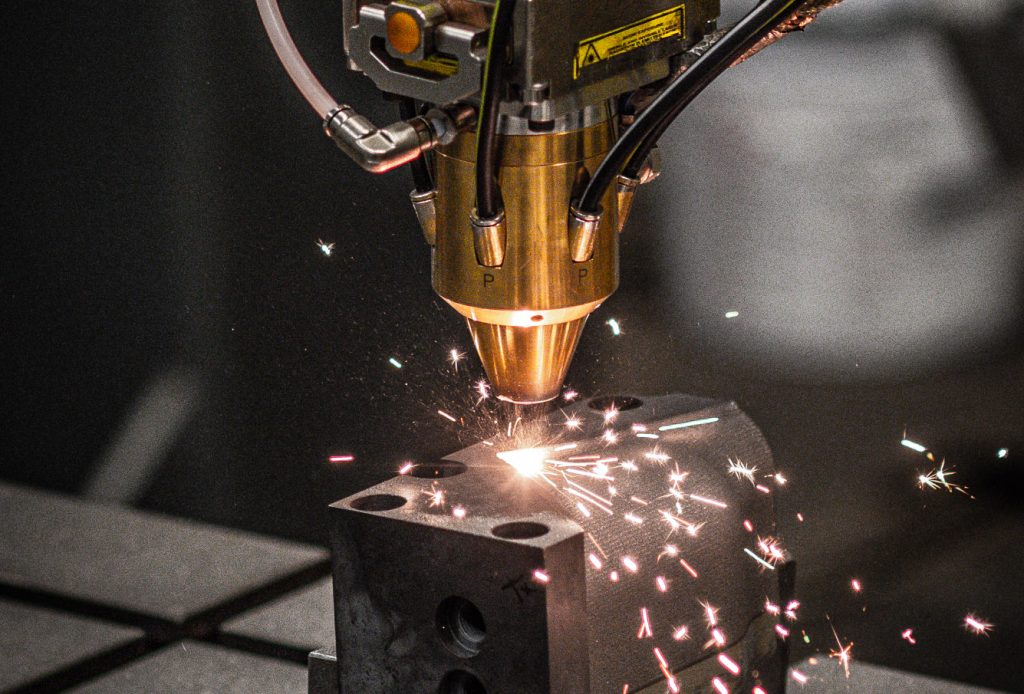
HOW DOES IT WORK?
The laser beam melts the base material, and ceramics/cemented carbides are pushed into the molten base material, which then solidifies rapidly.
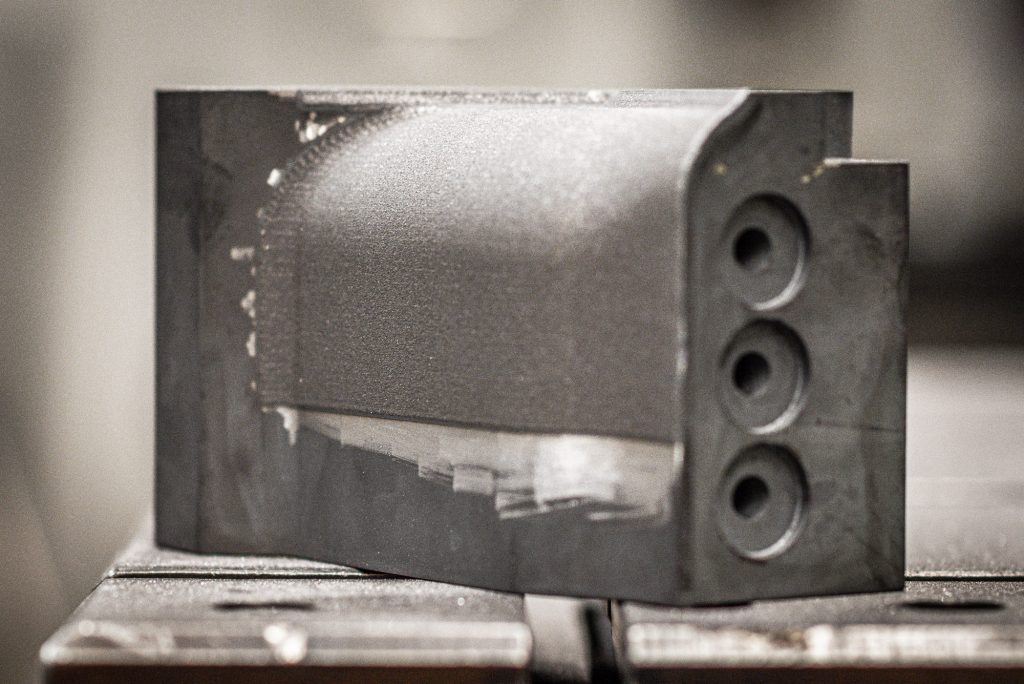
BENEFITS OF LASER IMPREGNATION
-
Very good properties for counteracting wear and tear. The hardness in the hard phase is above 3000 HV
-
Improved corrosion resistance during alloying with, for example, chromium
-
High or low friction depending on application and finishing
-
High load capacity on the surface layer